Mumbai’s Monorail project that was thrown open to the public on February 2, 2014, is not only the first monorail project in independent India but it has many design and engineering features seen for the first time in any mass rapid transit system in the country. A project by Mumbai Metropolitan Region Development Authority (MMRDA), the monorail was built by a joint venture of domestic engineering company Larsen & Toubro Ltd and Scomi of Malaysia. In a recent media briefing L&T highlighted some interesting and unprecedented features of the project, especially on the electrical and automation front.
Two business units of L&T’s Electrical & Automation (E&A) division – Electrical Systems & Equipment (ESE) and Control & Automation (C&A) — were actively involved in the project. While ESE provided the power supply and distribution, as well as the electrical and mechanical services, C&A put up the automatic fare collection system.
Electrical Systems and Equipment: Giving an overview of the electrical system of the Mumbai Monorail, a senior L&T engineer explained L&T-EA commissioned the entire electrical system including power distribution, DG sets, transformers, UPS systems, batteries and battery charges, luminaries, fire-fighting systems and HVAC systems.
Discussing the main power input, the official noted that power is received at 22kV and is distributed at the industrial voltage of 415V. Around 3km of underground cabling has been implemented with two receiving stations. Power is used for the traction system (running the monorail) and for the auxiliary system (running other facilities at the stations). There are four power lines in all and the system so created is that power supply is ensured even if just one of the four lines is functioning. Even if all the power lines are unavailable, DG sets will energize the traction system while the UPS system will provide auxiliary power.
Dwelling on the challenges, the official noted that the monorail system is at an elevation of at least 11m from ground level, and going up to 16m in some places. Among other things, laying cables for the traction system was a challenge. Unlike in elevated metro rail systems, where there is a “slab” on which a cable car could be rolled on, the guide beams of the monorail system (see picture) do not offer any space to stand or place any equipment. As an innovative solution, L&T devised a scaffold-like structure on either side of two successive columns. (The distance between two columns, known as the span, is 250m in the Mumbai Monorail project). Wires were pulled over the columns and placed under the guide beam. This process was repeated to cover the entire 9-km stretch. As the entire project is an elevated structure, lifting of equipment over a height of 11m to 16m, without disturbing pedestrian and vehicular traffic on the road, was a challenge that ran through the entire project.
Control & Automation: The C&A unit became the first Indian party to design, execute and maintain the automatic fare collection (AFC) system for any mass rapid transit system in India. The highly sophisticated and secure AFC system includes automatic gates, ticket vending machines, ticket vending machines, ticket readers, portable ticket decoders, station servers, central servers, etc. No consultant was hired while designing or implementing the AFC system, L&T officials pointed out.
Overview: Giving an overview of the business division, S.C. Bhargava, Senior Vice President, Electricals & Automation, explained that the E&A division clocked a turnover of around Rs.5,000 crore in FY14, accounting for 6 per cent of the sales turnover of Larsen & Toubro Ltd. The division includes LV switchgear, MV switchgear, standard components, energy meters, and control & automation. Even though electrical & automation accounted for only 6 per cent of the total project outlay of Mumbai Monorail (Phase 1), the division has done much through its automation systems to improve the quality and safety standards of the project, Bhargava noted.
Discussing the division further, Bhargava said that 30 per cent of L&T-EA’s turnover comes from outside India. The division has six factories in India and eight abroad. Acquisitions (e.g. Tamco in Malaysia) have helped in gaining product and geographic adjacencies, the business head noted.
Mumbai Monorail
The first phase of the Mumbai Monorail project was opened to public on February 2, 2014. It comprises a stretch of 8.93 km from Chembur to Wadala with seven stations including the extremities. The depot is located at Wadala. Phase-2 will extend for another 10.47 km from Wadala to Jacob Circle (officially known as Sant Ghadge Maharaj Chowk) with ten stations en route. When commissioned, the 19.4-km Mumbai Monorail will be amongst the longest monorail corridors in the world, by current thinking.
Photos: Venugopal Pillai
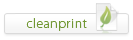
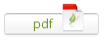
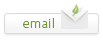